
Engineered for performance
Take your cutting to the next level with our end mills with the highest material removal rate on the market. Our end mills are designed to optimize your manufacturing processes by enabling you to combine remarkable vibration control, an excellent material removal rate, a perfect surface finish and unmatched durability.
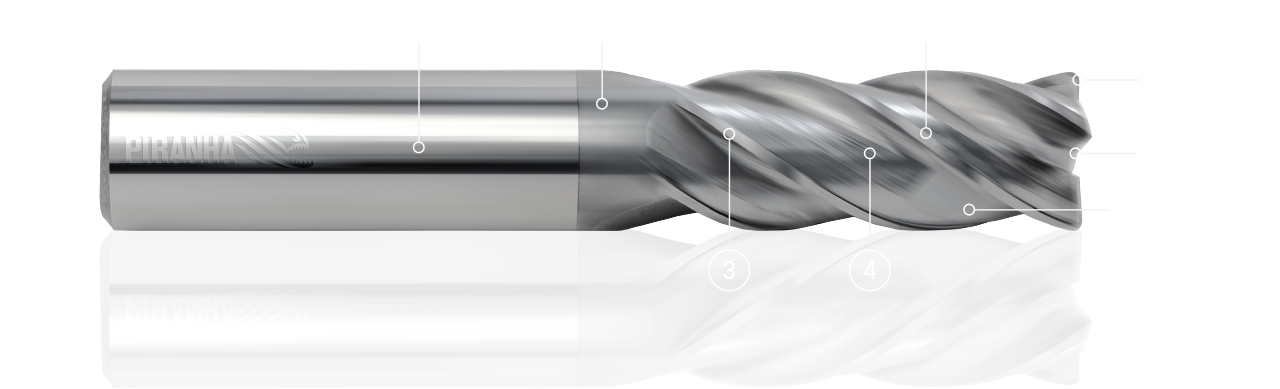
Micrograin structure to create sharp edges and thus resisting thermal and mechanical loads.
Nano-gradient coating ensuring optimal adherence, thermal resistance, a low coefficient of friction and great durability.
Helices with optimized angles and different from one another in order to reduce harmonics.
Larger lip depth on the end of the tool than at the end of the cutting length. This angle creates an optimized core diameter to counteract the forces generated and to ensure greater performance.
Optimal radius are applied to the cutting edge to eliminate micro-fissures which optimizes efficiency and increases the tool’s lifespan.
Non-isometric positioning of the flutes to reduce harmonics.
The radius are perfectly tangent to facilitate and optimize your manufacturing processes
The double cutting angle provides better chip breakage and optimum yield.
Carbide
Cutting tools must simultaneously withstand big mechanical loads and high temperatures. Temperature in the chip/tool interface reaches more than 700 °C in some cases.
Additionally, the friction between tool and removed chip, on one hand, and tool against the new machined surface, on the other, is very severe. Bearing this in mind, the main factors for a good tool design and postmanufacturing are:
- Cutting-tool substrate material must be very stable chemically and physically at high temperatures.
- Material hardness must be kept to the high temperatures suffered at the chip/tool interface.
- Tool material has to present a low wear ratio, both for the abrasion and adhesion mechanisms.
- Tool material must present enough toughness to avoid fracture, especially when operation to perform implies interrupted or intermittent cutting.

Coating
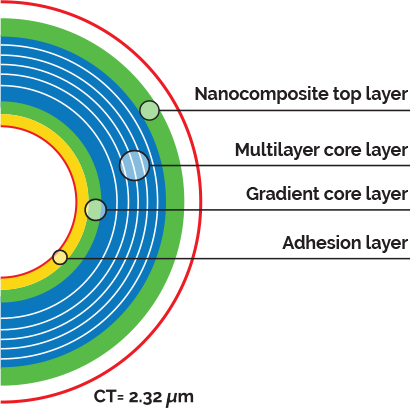
PVD coatings are very useful because of their high hardness, wear and oxidation resistance, thermal stability and lubricity.Gradient deposition nanotechnology provides improved adhesion to substrate and the coating-substrate system’s mechanical properties by eliminating the mismatch in material properties at the interface and reducing residual stresses. Gradient deposition nanotechnology reduces coating decohesion due to weak adherence. Nanocomposite gradient superhard coatings have superior performance under abrasive wear, erosive wear and impact wear.
Variable helix
The variable helix end mill has unequal flute spacing at various points along the tool’s cutting length. Unequal flute spacing helps dampen the vibration generated by the milling process. This vibration dampening enables faster feed rates and improved surface finishes. PIRANHA offers a variety of variable helix designs depending on the application.
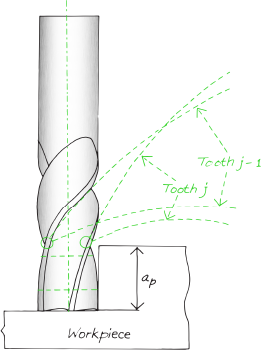
Core taper
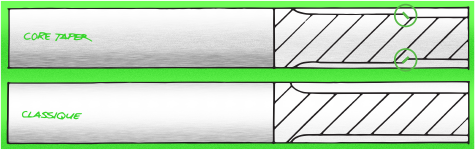
This redesigned geometry obtains maximum rigidity due to a larger flute section at a location where it experiences the most significant torque. This reduces the tool’s bending, which increases resistance to breakage and improves the material removal rate.
Edge prep
Edge prep prepares the edge of the tool for cutting at the main point of contact. This particular area is not always visible to the naked eye, but the difference soon becomes more noticeable through the machining process. Doing edge prep helps reduce stress risers, which are microscopic cavities that appear as a serrated edge under a microscope. During the machining process, those microscopic cavities create an area of stress. Stress buildup can contribute to the tool’s breakdown as well as its resulting work. Edge prep can also blunt the tool’s cutting edge keeping the tool in compression from the force of the cut.
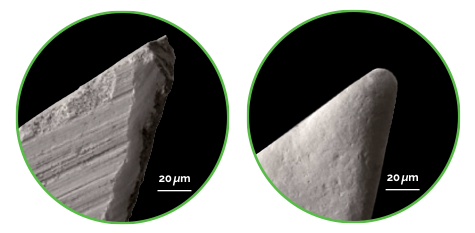
Unequal indexing
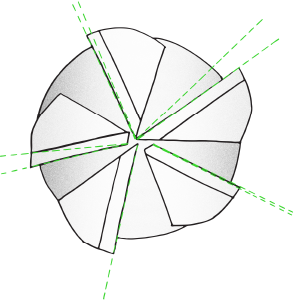
The unequal indexing end mills' configuration enables high-performance machining by minimizing the harmonics created by the high forces generated during the process. By shifting the moment of impact of the opposing teeth, the forces are then more evenly distributed, thereby reducing vibration as well as the amplitude of the shockwaves.
Tangential radius
PIRANHA has committed to manufacture cutting tools providing tangential radius for a higher level of precision worthy of the aerospace industry. By guaranteeing this precision, PIRANHA tool users benefit from improved manufacturing times by avoiding the finishing process. The result is a more precise finish, for REDEFINED PERFORMANCE.
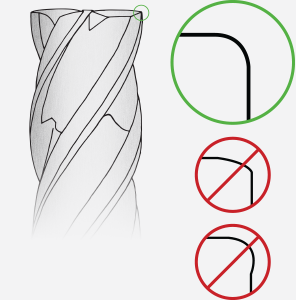
Double-rake
The PIRANHA tools double rake configuration enables material to be fiercely attacked at a high material removal rate thanks to its two distinct rakes, which enable chip breakage and prevent jamming the flutes. These tools can therefore be used on very hard materials and/or on those with very low machinability rating such as exotic materials. VERY HIGH PERFORMANCE tools.
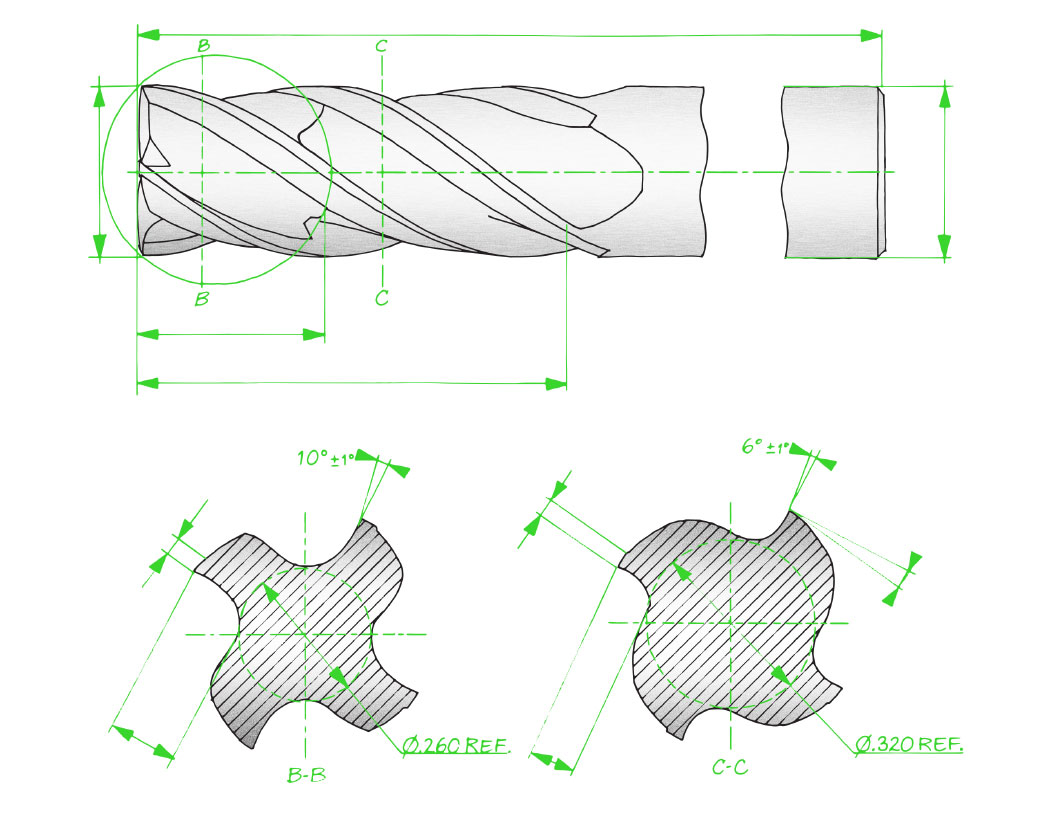